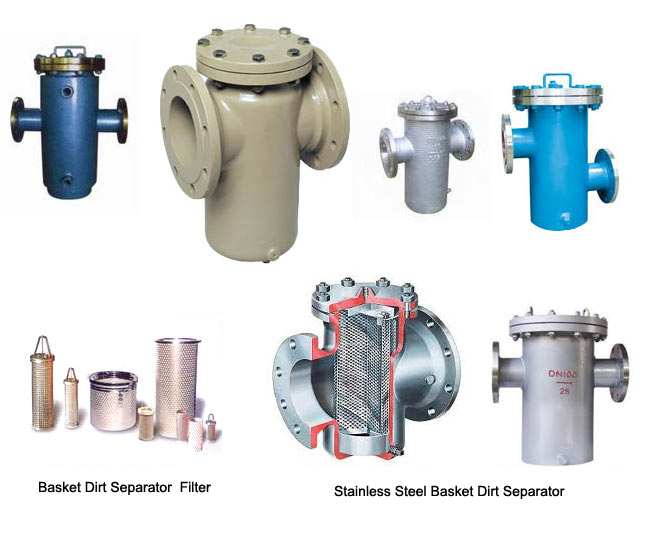
Overview: Basket dirt separator is used on oil pipelines or other liquid pipelines, to filter out impurities in pipes. Its filtration slit area is 2-3 times larger than the area of a pipe, and far exceeds the filtering area of Y-shaped filter and T-shaped filter. Basket filter has the highest filtration precision among filters; its filter screen is different from that of other filters, shaped like a basket. This is why it is called basket dirt separator.
Basket dirt separator is mainly constituted by a connecting pipe, a cylinder, a strainer basket, flanges, blind flanges, and fasteners. Installed on pipelines, the basket dirt separator removes large solid impurities from liquids, ensures normal operation of machinery equipment (including compressors and pumps) and instruments, achieves stable processes, and guarantees safe production.
Working Principle: Impurities will be carried into pipelines during installation; and raw materials of pipes also contain impurities. When liquids flow through the filter, impurities therein will be filtered out into the filter screen. When necessary, remove the cover to clean the filter screen.
General Principles for Selection of Dirt Separator: 1. Outlet and Inlet Diameter: In principle, filter outlet and inlet diameter shall not be less than the inlet diameter of the assorted pump, generally, the same as the inlet pipe diameter. 2. Nominal Pressure: Pressure grade of filter is determined according to the possible maximum pressure of the filter pipe. 3. Screen Number: Particle diameters of the impurities to be filtered out shall be taken into consideration; and the screen number shall be determined in accordance with process requirements for the media. For particle sizes able be filtered out by different specifications of screen mesh, see the following table Filter Screen Specifications.
Technical Parameters: 1. Applicable materials: a. Weak corrosive materials in chemical and petrochemical production, such as water, ammonia, oil products, and hydrocarbons, etc. b. Corrosive materials in chemical industry, such as sodium hydroxide, sodium carbonate, dilute sulfuric acid, carbonic acid, acetic acid, and stearic acid, etc. c. Low-temperature materials for refrigeration, such as liquid methane, liquid ammonia, liquid oxygen and various refrigerants; d. Materials with hygiene requirements in food and light industry and pharmaceutical industry, such as beer, beverage, dairy products, and medicines, etc. 2. Working temperature: -80 +450 3. Nominal diameter: DN15DN600 4. Nominal pressure: PN1.05.0Mpa 5. Flange standard: HG20592-97 (or in accordance with customer requirements) 6. Body material: A3, 304, 304L, 316, 316L 7. Sealing material: polyfluortetraethylene, nitrile rubber, and oil-resistant asbestos rubber 8. Manufacturing inspection standard: HGJ532-91 |