Sponge iron deaerator is a kind of deaerating plant. Oxygen-containing water enters into the deaerator, and flows through the sponge iron filter media layer. The special sponge iron filter media, with huge specific surface area, may realize complete oxidation of the dissolved oxygen in water and iron, thus removing oxygen from water.
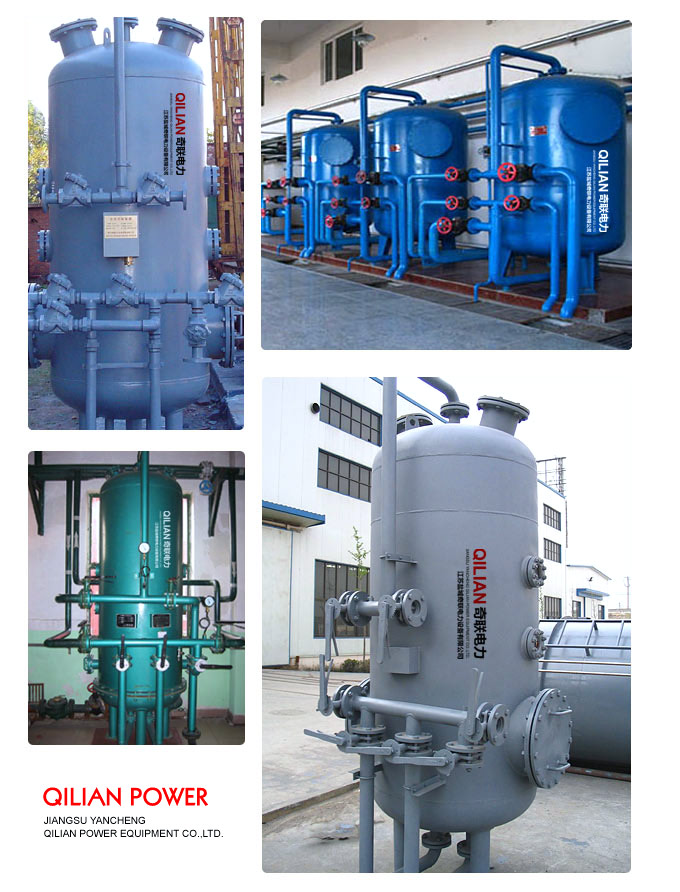
1. Working Principle Normal-temperature filtration deoxidation belongs to chemical deoxidation. Special activated sponge iron (direct-reduced iron) is used to remove dissolved oxygen from water. Sponge iron consists mainly of iron. Its loose porous inner structure provides 5-10 times the specific surface area of ordinary iron scraps, enables complete oxidation of oxygen in water and iron, and maintains the content of dissolved oxygen below 0.05mg/L. Relevant reaction formulas: 2Fe2+ + 2H2O + O22Fe(OH)2 4Fe(OH)2+ 2H2O +O24Fe(OH)3 Reaction products Fe(OH)2 and Fe(OH)3 are flocculent precipitates which are not easy to dissolve in water; they will be held up when flowing through the rest sponge iron particles, and can be washed out with a certain intensity of backwash water (about 5min).
The consumption of sponge iron is very low, which varies according to the volume and quality of the treated water; sponge iron is generally replenished every 3-6 months. (After deoxidation, there will be a small additional amount of ferric ion, usually 0.2-0.5mg/L, which conforms to national water quality standard for hot-water boilers; however, for steam boilers or feed water deoxidation with strict requirements for Fe2+ concentration, an iron removal device can be added to remove Fe2+ from water)
As a water oxygen scavenger, sponge iron particles are bonded together through Fe3O4 powders whose particle size is less than -200 mesh; the particle size of sponge iron is about 2-5mm. The oxygen scavenger has high porosity and large specific surface area, because a certain number of air gaps are formed in replacement reaction during its reduction process, and there are many air gaps between the powder particles. Besides, the oxygen scavenger is relatively pure and clean, since it is obtained through direct reduction of iron ore. Therefore, sponge iron has high activity, and is extremely easy to react with oxygen in water and generate Fe3O4. Thus, oxygen is removed from water. Its utilization rate is as high as 90% and above. Meanwhile, the oxygen content of the outlet water is lower than 0.05mg/L. Treating a cubic meter of water only needs approximately 25g of sponge iron, which realizes high quality and low cost in the real sense.
Because unsoftened water is easy to cause surface passivation of oxygen scavenger, slow down oxidation, and influence the effect of deoxidation, water shall be softened before being deoxidized. Sponge iron shall be backwashed after being used for a period of time.
2. Characteristics of Sponge Iron Deaerator 1) Deoxidation can be realized at ordinary temperature; inlet water does not need to be heated; 2) The system may provide water supply at any time and does not need preparation time or deaerator tank; 3) The effect of deoxidation is stable and reliable; the dissolved oxygen content of outlet water is stable, 0.05mg/L, in conformity with the water quality standard for low pressure boilers; 4) There are no special requirements for installation; the equipment overcomes the inconvenience of high-level installation required by thermal deaerators and vacuum deaerators; 5) The equipment can be installed in a low position; with simple operation and no special height requirements.
Model |
Volume of Water Treatet/h |
mm
|
H mm |
H1 mm |
H2 mm |
Inlet and Outlet DN |
Forward Flush OutletDN |
Backwash Outlet DN |
Weight of Packing Materialkg |
Height of Packing Material Layermm |
QL-GLQ-101A |
4 |
450 |
2800 |
1100 |
700 |
40 |
40 |
50 |
330 |
680 |
QL-GLQ-201A |
6 |
600 |
2800 |
1100 |
750 |
40 |
40 |
65 |
580 |
950 |
QL-GLQ-301A |
10 |
700 |
2900 |
1200 |
800 |
50 |
50 |
80 |
780 |
1250 |
QL-GLQ-401A |
15 |
900 |
3050 |
1200 |
800 |
65 |
65 |
100 |
1350 |
2300 |
QL-GLQ-501A |
20 |
1000 |
3100 |
1250 |
800 |
80 |
80 |
125 |
1800 |
2700 |
QL-GLQ-601A |
25 |
1100 |
3150 |
1300 |
850 |
80 |
80 |
125 |
1950 |
3000 |
QL-GLQ-701A |
30 |
1200 |
3200 |
1400 |
900 |
100 |
100 |
150 |
2300 |
3750 |
QL-GLQ-801A |
40 |
1400 |
3300 |
1400 |
900 |
100 |
100 |
150 |
3150 |
4200 |
Control Mode |
Manual or full-automatic control (automatic control type needs a control cabinet, an electrically operated valve, and a differential pressure gauge) | |